
Understanding PMI Foam: A Deep Dive into Its Classifications and Applications
Polyisocyanurate-methacrylimide (PMI) foam has emerged as a cornerstone material in industries where high strength-to-weight ratios, excellent mechanical properties, and thermal stability are paramount. From the wings of an aircraft to the core of a wind turbine blade, PMI foam offers unparalleled performance. However, PMI foam isn't a one-size-fits-all solution; it comes in various classifications, each engineered for specific performance requirements and manufacturing processes. Understanding these classifications is key to unlocking its full potential in your demanding applications.
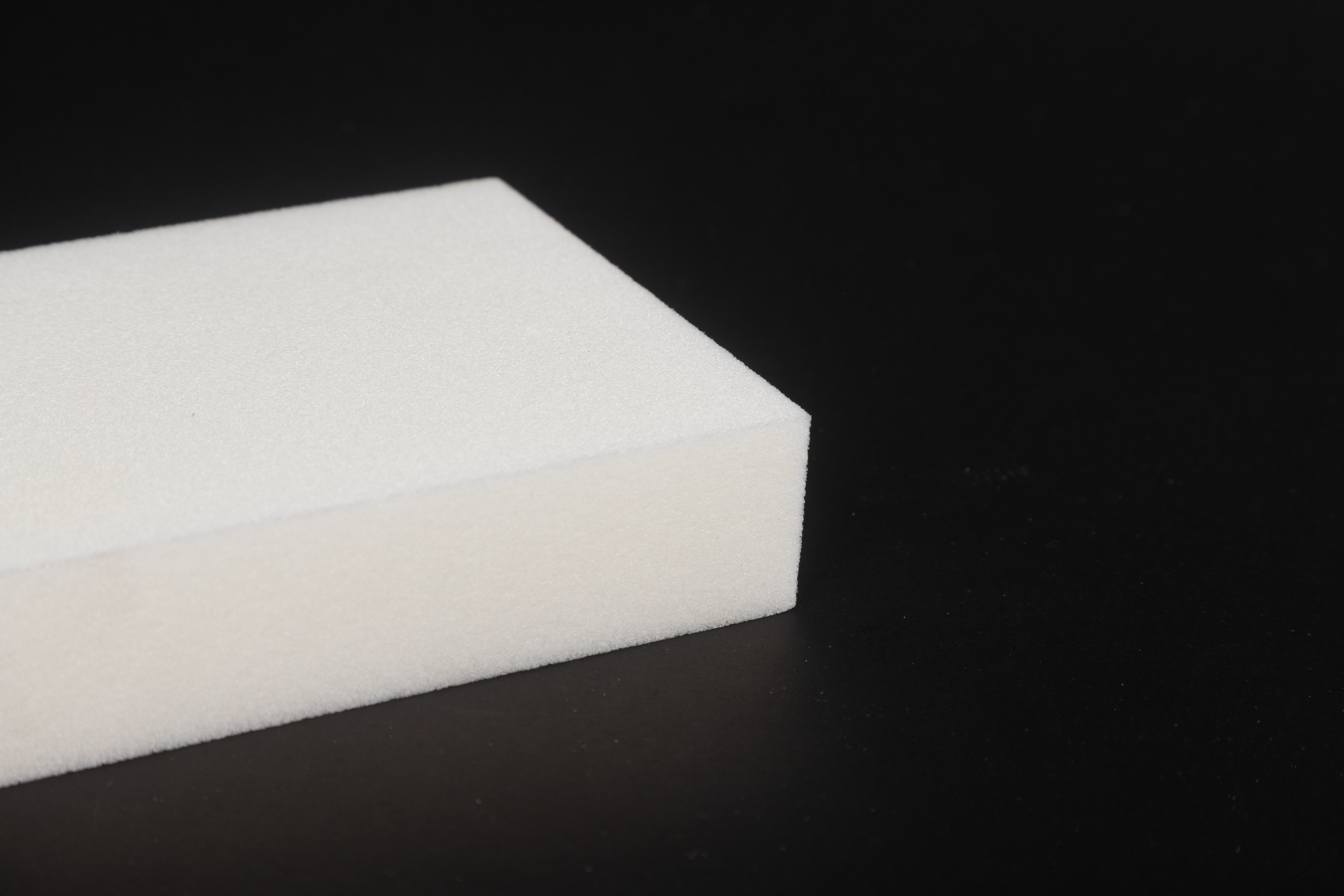
The Primary Classifications of PMI Foam
PMI foam is primarily classified based on its density and, consequently, its mechanical properties. While manufacturers may have proprietary naming conventions, the core principle remains consistent: higher density generally correlates with higher strength and stiffness.
1. Low-Density PMI Foams (e.g., 30-70 kg/m³)
These foams are at the lighter end of the spectrum, offering exceptional weight savings. They are typically used in applications where minimizing mass is the absolute top priority, and the structural loads are moderate.
- Characteristics: Excellent specific strength (strength-to-weight ratio), good shear properties, and often easier to machine due to their lower density.
- Typical Applications: Fairings, interior panels in aerospace, radomes, and recreational sporting goods where weight is critical for performance (e.g., high-performance skis or surfboards).
2. Medium-Density PMI Foams (e.g., 70-130 kg/m³)
Representing a versatile middle ground, medium-density PMI foams strike an excellent balance between weight and mechanical performance. This makes them suitable for a vast array of structural applications.
- Characteristics: Balanced mechanical properties, good fatigue resistance, and excellent compatibility with various resin systems. They offer a significant step up in compressive and shear strength compared to lower-density variants.
- Typical Applications: Aircraft primary and secondary structures (e.g., floor panels, control surfaces), automotive body panels, marine bulkheads, and industrial tooling.
3. High-Density PMI Foams (e.g., 130-200 kg/m³ and above)
These are the workhorses for highly loaded structures. High-density PMI foams provide the highest mechanical strength and stiffness, capable of withstanding extreme stresses and strains.
- Characteristics: Superior compressive strength, high shear strength, and excellent dimensional stability under high loads. They are robust and ideal for demanding structural components.
- Typical Applications: Wind turbine blades (especially the root section), helicopter rotor blades, highly stressed aerospace components, and specialized industrial applications requiring maximum rigidity and load-bearing capacity.
Beyond Density: Other Important Classifications and Considerations
While density is the primary classification, other factors also play a role in defining specific PMI foam grades:
- Pore Size: As discussed in previous contexts, the size of the individual cells within the foam can influence resin infusion characteristics and subtle mechanical properties.
- Processing Temperature: Some PMI foams are optimized for higher processing temperatures, making them compatible with advanced composite manufacturing techniques like prepreg curing or resin transfer molding (RTM) at elevated temperatures.
- Flame Retardancy: For specific applications, particularly in aerospace and public transportation, PMI foams with enhanced flame retardant properties are available to meet stringent safety regulations.
- Perforation/Grooving: Some PMI foams come pre-perforated or grooved to facilitate easier resin flow during infusion processes, further optimizing manufacturing efficiency.
Choosing the Right PMI Foam Classification
Selecting the ideal PMI foam classification involves a thorough understanding of your project's specific needs. Consider the following:
- Structural Loads: What are the expected compressive, tensile, and shear forces the component will experience?
- Weight Targets: How critical is weight reduction to the overall performance and efficiency of the final product?
- Manufacturing Process: What resin system and curing temperatures will be used? How important is efficient resin flow?
- Environmental Conditions: Will the component be exposed to extreme temperatures, moisture, or other aggressive elements?
- Cost-Benefit Analysis: Balancing performance requirements with material cost and manufacturing complexity.
By carefully evaluating these factors, engineers can precisely match the right PMI foam classification to their design, ensuring optimal performance, manufacturing efficiency, and cost-effectiveness for their advanced composite structures.
PMI foam
Latest News