
PMI Foam: Elevating Drone Propeller Performance
The world of drones is rapidly evolving, with advancements in design and materials constantly pushing the boundaries of performance. At the heart of every drone's flight are its propellers, crucial components that dictate efficiency, speed, and maneuverability. While carbon fiber has long been the go-to material for high-performance propellers, a lesser-known but increasingly vital material is gaining traction: PMI foam. This high-performance polymer foam, specifically polymethacrylimide, is revolutionizing how drone propellers are designed and manufactured, offering a unique blend of strength, stiffness, and lightweight properties.
What is PMI Foam and Why is it Ideal for Propellers?
PMI foam is a rigid, closed-cell foam with an exceptionally high strength-to-weight ratio. It's often used as a core material in sandwich composites, where it's typically faced with thin, strong skins like carbon fiber. This construction method allows for the creation of incredibly stiff and strong structures without adding significant weight.
For drone propellers, these characteristics are paramount. Propellers experience immense centrifugal forces and aerodynamic stresses during flight. Traditional solid carbon fiber propellers, while strong, can be heavy, which directly impacts flight time and payload capacity. PMI foam offers a solution by:
- Reducing Weight: By using PMI foam as a core, manufacturers can significantly reduce the overall weight of the propeller without compromising structural integrity. Lighter propellers mean longer flight times and increased payload capacity, crucial for commercial and industrial drone applications.
- Enhancing Stiffness and Vibration Damping: The rigid nature of PMI foam contributes to a stiffer propeller. A stiffer propeller experiences less flex and deformation during high-speed rotation, leading to improved aerodynamic efficiency and reduced vibrations. Less vibration means a smoother flight, better image stability for cameras, and less stress on the drone's motors and electronics.
- Improving Fatigue Resistance: The unique cell structure of PMI foam provides excellent resistance to fatigue, a critical factor for components subjected to repetitive stress cycles like propellers. This translates to a longer lifespan for the propellers and increased reliability.
- Facilitating Complex Geometries: PMI foam can be easily shaped and machined, allowing for the creation of complex and aerodynamically optimized propeller designs that might be challenging or costly with solid materials. This opens up new possibilities for improving propeller efficiency and reducing noise.
PMI Foam in Propeller Manufacturing
The integration of PMI foam into drone propellers typically involves a sandwich construction. A thin layer of carbon fiber composite is often laid up over a precisely cut PMI foam core. This assembly is then cured under heat and pressure, bonding the carbon fiber skins to the foam core. The result is a lightweight, incredibly rigid, and durable propeller that outperforms many traditional designs.
The Future of Drone Propellers with PMI Foam
As drone technology continues to advance, the demand for even lighter, stronger, and more efficient components will only grow. PMI foam is well-positioned to meet these demands. Its unique combination of properties makes it an ideal material for the next generation of drone propellers, enabling longer flights, higher payloads, and improved overall performance. Expect to see PMI foam become an increasingly standard material in high-performance and commercial drone applications, pushing the boundaries of what these incredible machines can achieve.
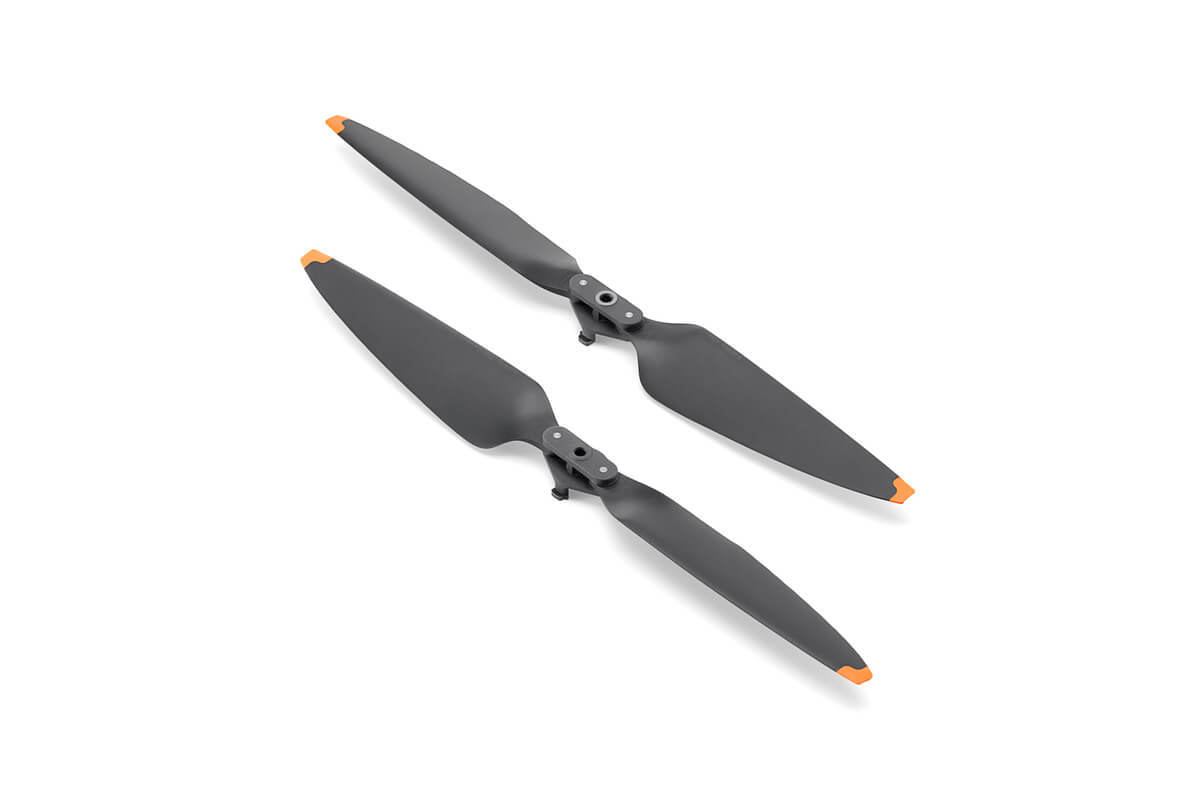
PMI foam
Latest News
Previous Page